Software Interface for Material Database to COMSOL® Material Library
The use of advanced manufacturing technologies expands the design scope of lightweight components for aerospace systems and enables innovative possibilities for complex structures [1, 2]. The overall approach of the AdHyBau (Additive Hybrid Construction) joint project is to develop new additive processes and fiber composite-metal hybrid structures for use in the cryogenic environment of an aerospace electric powertrain using liquid hydrogen for cooling and power generation. Goal of the project is to create end-to-end design and simulation processes to represent reality as accurately as possible in a digital twin. The general design and simulation of the powertrain within the framework of a digital twin is being carried out by Siemens AG [3], while components of the electric motor are being investigated by Siemens AG together with the Institute for Lightweight Construction and Plastics Technology at TU Dresden [4]. The hydrogen system for storage, distribution and utilization is developed and optimized by MT-Aerospace AG [5]. Material investigations are carried out at KIT together with the Fraunhofer Institute for Materials Engineering [6]. In order to combine the simulation process of the electric hydrogen propulsion system through a digital twin with real data, the material properties are compiled in a database file. To incorporate the data into finite element method (FEM) software such as COMSOL®, a Python script was created to read the data and, if necessary, convert the information into a file readable by the FEM software as a three-dimensional tensor. The material properties are included in the general material library of the system and can be selected according to the desired additive manufacturing process (CS, SLM, DED) and treatment condition (e.g. for copper according to RRR value). This allows direct physical coupling in the calculations of the different components in terms of mechanical or thermal behavior. Still open challenges are the 3D material properties and uncertainty incorporation. Interfaces for other FEM software are in preparation.
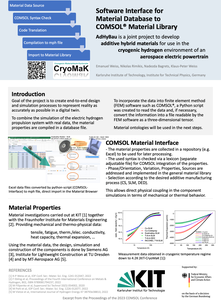
Téléchargement
- Weiss_7361_poster.pdf - 1.23MB