Simulation of the Flow of an Autonomous Spherical Ball inside a Pipeline
One of the limitations of pipelines performance and structural integrity assessment is the continuous inspection of possible leaks due to corrosion or other types of failure mechanisms. Efforts to develop new technologies started several decades ago where different inspection techniques were used to enhance pipelines structural integrity. However, although available technologies present some advantages, they still have some limitations in practice. This paper presents numerical simulation results of an initial study that aims at developing a new inspection technique consisting of inserting an autonomous self-recharging spherical ball, equipped with multiple sensors, and moving inside the pipeline for inspection. The simulation initially concentrated on the fluid flow around the spherical ball and noise level propagating inside the pipeline. The COMSOL Multiphysics® software was first used to create the geometry of this autonomous ball, which presents a novel design in mobile inspection tools. Then, the Computational Fluid Dynamics (CFD) Module was used to simulate the velocity and pressure propagation around the ball inside the pipeline before and after a leak had occurred. The goal of using the CFD Module is to find the velocity and pressure profiles around the moving ball. Next, the Acoustics Module was used to simulate the leak noise propagation generated when a leak occurs. A point source was created at the wall of the pipe and was assigned a power of 1W which is equivalent to 30 dB. That value was obtained experimentally using a flow loop having open holes of various sizes to mimic leaks from which the sound level was measured using acoustic sensors. The goal of using this module was to see how leak noise travels inside a pipeline and how it propagates around the mobile ball. The results intended will be used to provide enough data to build a control system able to detect leak sizes and locations with higher precision. In addition, the COMSOL® software will be used to conduct a sensitivity analysis such as fluid type, pump pressure or leak position effect on the fluid flow profiles (velocity, pressure and acoustic propagation inside the pipe).
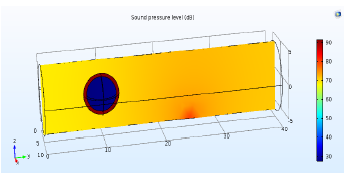
Téléchargement
- chalgham_presentation.pdf - 1MB
- chalgham_poster.pdf - 0.42MB
- chalgham_paper.pdf - 0.99MB
- chalgham_abstract.pdf - 0.15MB