Simulation of Lattice Structures in Orthopedic Corsets
Digitization is affecting more and more industrial sectors. In the field of orthopedic technology, new technologies such as 3D scan and 3D printing are used in production. This opens up new fields of application for the simulation. The example of a scoliosis corset shows how the new technologies intertwine and enable new, individualized products. Scoliosis refers to a spinal curvature that often occurs in girls during adolescence. Depending on the severity, corsets are also used for therapy. The corset production according to the prior art with plaster cast is done by hand and is very complex (Fig. 1). 3D Scan / 3D printing enables new, customized designs, e.g. with breathable lattice structures (Fig. 2). As a result, the wearing comfort and acceptance can be increased, which has a positive effect on the success of the therapy. In the simulation, the stresses / strains and forces occurring when opening the corset are of interest (Fig. 3). The maximum force when putting on and taking off the corset must not be exceeded. Also the yield strength of the plastic used must not be exceeded. Models with lattice structures pose a challenge during import and meshing, as they are usually not available as surface CAD models but as fine surface STL meshes. The handling of such fine meshes with often several hundred MB filesize is difficult. When importing, there are often mesh errors such as self-penetrating surfaces. For 3D meshing with tetrahedra, these errors must be repaired and transformed into a solid model. In order to be able to apply suitable boundary conditions, partitioning is also required. These steps are performed in the COMSOL Geometry and Mesh module. For the material an elastic-plastic characterization is used and the structure is calculated with large deformations. In postprocessing the max. stress / strains and forces are evaluated. Based on the results, the corset and grid dimensions can be iteratively adjusted to meet the specifications. Comsol enables fast design verification in the virtual stage and reduces time-consuming testing.
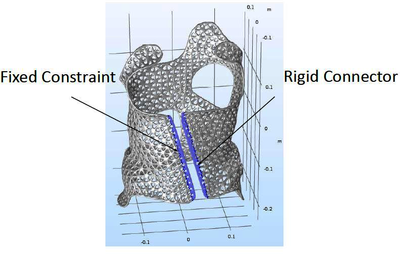
Téléchargement
- rieder_poster.pdf - 0.85MB
- rieder_paper.pdf - 0.67MB
- rieder_abstract.pdf - 0.08MB