Predicting Fatigue Life of Cold-Sprayed Multi-Materials and Functionally Graded Materials
Cold Spray Additive Manufacturing (CSAM) involves accelerating fine particles in a gas stream through a de Laval nozzle, which then impacts a substrate, creating a metallurgical bond with low thermal impact. This can be done with metals, alloys, composites, and ceramics. CSAM technology has rapidly gained prominence due to its ability to create near-net shape components, large-scale additively manufactured components, and materials with tailored properties for coatings and repairs. By blending powders, “multi-materials” can be created with customized properties. Similarly, Functionally Graded Materials (FGMs) can be made by gradually changing the powder composition through the spray process. Triton aims to define the fatigue properties of cold-sprayed multi-materials and FGMs from static mechanical test inputs in this investigation.
The objective of the model setup is to determine cyclic loading responses and lifetime predictions of certain multi-material or FGM CSAM processed material properties using input from static experiments. Running a lifetime fatigue model of multiple coupons experimentally is timely and costly. The COMSOL Multiphysics® Fatigue Module offers faster predictions to determine the stresses within a system due to a lifetime of load cycles.
For this model, an ASTM E290-22 dog-bone is subjected to cyclical stress, mimicking ASTM E466-21 fatigue loading conditions. Fatigue loading conditions require a high-cycle model characterized by repeated elastic deformation. The loading conditions are proportional as the orientation of the principal stresses and strains does not change during the load cycle. A stress life model generates an output of cycles per lifetime of the multi-material and FGM components. The results are first validated using COMSOL’s Structural Mechanics Module to benchmark the static experiments. Then, fatigue life predictions are compared with experimental data.
This model's unique spin on the fatigue analysis is incorporating graded properties for the FGM CSAM materials in the dog-bone specimens. These materials are made up of different ratios of powder, resulting in a range of material properties. FGMs contain spatial variation in their composition. To demonstrate their unique material properties, a custom coordinate system is used to define the material locally. The material properties are calibrated from experimental results, which can be exprobated to determine fatigue conditions.
Cold spray has been widely accepted for coatings and repairs, but more investigations are necessary to validate that CSAM can build structural load-bearing components. Triton’s fatigue studies using COMSOL enable the investigation of multi-material and FGM CSAM components in cyclic load-bearing scenarios to contribute to this field of research. Moreover, they enable the optimization of multi-material blends or FGM gradients for numerous applications. These analyses have implications for the aerospace, energy, transportation, electronics, and power industries.
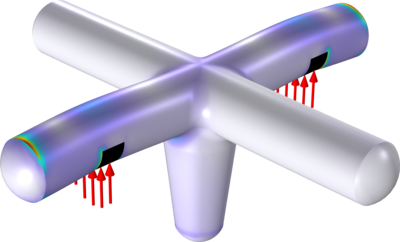