Powder consideration for additive manufacturing simulation
As additive manufacturing for metallic material is more and more used in industry, researchers try to overcome the limits of the process. To improve this industrial process, in terms of applications and understanding, the numerical simulation is today a very strong tool. Nevertheless, Laser Powder Bed Fusion is one of the most complex applications considering continuous wave lasers and tends to produce defects as spatters, denudated areas or instabilities. The beams are quite thin (<100 µm), the powder has micrometric characteristic sizes and the feeding rates can be very larger than classical welding cases (>1m/s). Moreover, the high-power density of the process produces a quite strong vaporization phenomenon leading to liquid-gas interface deflection and fast gas ejection. In this paper, authors propose a thermo-hydrodynamic simulation of the gas atmosphere, the powder and the substrate materials in static (figure 1) and moving (figure 2) laser configurations. A realistic powder bed is set in the model thanks to powder spatial distribution and particle radii coming from another numerical analysis (Discrete Element Method). Particles are introduced in the COMSOL Multiphysics® simulation analytically through Java programming. The metal-gas interface is tracked by the Eulerian Phase-Field method. Authors discuss advantages and limitations of this method for mesoscale (size of the molten pool) thermal and fluid flow analysis compared to previous ALE works.
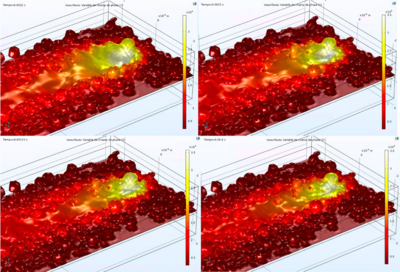
Téléchargement
- Paper_COMSOL_dal_3.pdf - 12MB
- Europe_2020_Poster_Dal.pptx - 6.85MB