- Bridging the Terahertz Gap
- Modeling the Lithium-Ion Battery
- Protection contre la Corrosion
- Modélisation des batteries
- Modélisation et Simulation dans le développement des piles à combustible
- Modélisation thermique des petits satellites
- Analyse électro-vibroacoustique d'un transducteur à armature équilibrée
Parameter Extraction for a Field Weakening Operation Model of a PMSM
INTRODUCTION: A key parameter for electrical engines is the power density. High power density is particular beneficial for traction drives. Accordingly, optimizing power density is essential for competitive ability in the Formula Student Electric racing series [1].
The operating principal of the Permanent Magnet Synchronous Machine (PMSM) allows for extending the power range without changing the geometry and therefore keeping constant mass [2]. The operation mode which enables this is called field weakening [3]. Figure 1 shows the torque-speed characteristic of a PMSM with and without field weakening operation.
The technique requires motor control. Several engine parameters are necessary for control implementation [3]. Since these parameters are also related to the motor dimensions they have to be available during machine design. In the past years several papers are published on how to use COMSOL Multiphysics® software for simulating different aspects of electromagnetic engines [4, 5, 6]. However, in this work COMSOL is used to extract the parameters required for field weakening motor control.
USE OF COMSOL MULTIPHYSICS: Figure 2 displays the components and geometry of the simulated PMSM. It corresponds to a motor variant which is currently designed by the Augsburg student racing team [1]. The simulation model is setup on the basis of the Rotating Machinery, Magnetic physics interface. For numeric efficiency the 2D geometry of Figure 2 is used. Regarding material, nonlinear H-B characteristics are used for the rotor and stator steel and also for the permanent magnet (PM).
As the motor rotates, it creates a back-EMF voltage across its coils proportional to the speed of rotation [3]. The constant of proportionality is determined by a particular model setup. Another model setup is used to determine the exact rotor positions for the q- and d-axis. This information is required for simulations performed to extract the phase inductances corresponding to those positions. In this work, the measuring method described in [7] is adapted for simulation. In particular the effect of nonlinear PM is taken into account. By performing a transient simulation with harmonic current excitation, the inductance-over-current character characteristic is obtained. An additional transient study with appropriate current excitation allow for characterizing the torque ripple.
RESULTS: Figure 3 shows an example of simulated magnetic flux density for the rotor in the q-axis position. In the paper the method to extract the phase inductance from that simulation result is described in detail. The basic idea is to extract the coil flux from the simulated tooth flux. The PM-flux has to be taken into account regarding the nonlinear H-B behavior of the steel. Applying the method proves results as shown in Figure 4. In the final paper the methods for extracting all relevant parameters will be presented.
CONCLUSION: Simulation is a powerful tool during the design process of a PMSM for a Formula Student Electric racing series engine. Using the Rotating Machinery, Magnetic interface enables efficient model setup to extract the required parameters for the field weakening motor control.
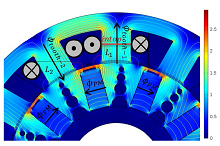
Téléchargement
- frey_paper.pdf - 0.56MB
- frey_abstract.pdf - 0.32MB