Numerical Simulation of Optimization of Process Parameters of Micro Wire EDM of Al-SiC Alloys Using COMSOL Software
Micro Wire EDM (Electro Discharge Machine) process is a highly reliable and non-conventional process to manufacture precise and accurate complex shapes in various types of conducting materials. The accuracy of this process is measured in micrometres, thus making it superior to other manufacturing processes. A need for achieving desirable properties like high strength, corrosion resistance, high melting temperature, etc., has resulted in various metal alloys and composites to come into being. Of such materials, Aluminum Silicon Carbide composites (Al-SiC) have proven to be of great interest in the field of research. Due to their exceptional properties like high specific strength, high thermal conductivity, less weight and so forth, they are being used in various industrial applications like electronic packaging, and also in automobile, aerospace, defense sectors. Thus, this paper aims at producing a numerical model of micro machining of various compositions of Al-SiC alloys and studies the effects of various parameters on machining such composites. This Finite Element Method (FEM) study is done by using the COMSOL Multiphysics software. A three dimensional model is considered for the analysis of the process. Temperature dependent properties like specific heat capacity, thermal conductivity have been taken into consideration. The heat source is assumed to be a Gaussian distribution on the surface of the model. The distribution of temperature on the surface and the effect of various parameters like input current and wire feed rate have been studied on various compositions of Al-SiC composites. These are then compared to the experimental results which have shown a good agreement with the predicted results.
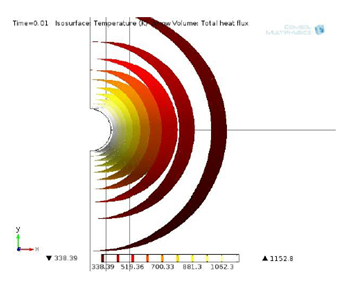
Téléchargement
- dheeraj_poster.pdf - 0.45MB
- dheeraj_paper.pdf - 0.64MB
- dheeraj_abstract.pdf - 0.23MB