Multiphysics Analysis of a Thermo-Acoustic MHD Inductive Generator
Magneto-Hydrodynamic (MHD) power generation systems were originally investigated starting from the fact that the interaction of a plasma with a magnetic field must take place at much higher temperatures than could be observed in a mechanical turbine. The main problems of traditional MHD generators are the high temperatures, and the high magnetic field (about 5 T), required to have significant outlet energy.
This paper fits in the feasibility analysis of a MHD inductive generator, coupled with a Thermo Acoustic (TA) resonator (Fig. 1). The MHD process and the TA processes has the great advantage to convert energy without mechanical moving components. The proposed device does not require an external magnetic field to work, on the contrary it performs the energy conversion through the induction principle. The charge carriers are at a first stage created by means of an electrical discharge and then separated by an external, high voltage electrostatic field. Once the equilibrium is reached, if the gas inside the duct starts vibrating as a result of the TA phenomenon, the charge carriers give rise to an alternating electric current in the fluid; this current induces an electromotive force in a toroidal coil wrapped around the duct and connected to the load.
Given the design criteria (Fig. 2), a FEM analysis has been performed to simulate the system functioning. First of all, an acoustic analysis has been done in order to study the velocity profiles within the duct. Differently than in lossless acoustics, the thermo-acoustic formulation takes into account viscous and thermal dissipative effects, which cannot be neglected in acoustic wave propagation through narrow geometries. A homogeneous fluid, with no steady flow, and sinusoidal perturbations of small amplitude (no circulation and no turbulence), has been considered. Moreover, the tube is long enough to neglect the end effects. Different velocity profiles were obtained by varying the frequency of the vibration. The numerical results confirm the theoretical ones retrieved from the literature. The axial velocity shows a parabolic profile for a low shear wave number; for higher values of the parameter the velocity becomes smaller in the center and the profile becomes more uniform. For very high values of shear wave number, the profile is almost completely flat, with small peaks close to the tube wall.
Furthermore, a simulation in COMSOL Multiphysics® software has been performed in a glass tube containing a ionized gas, by coupling the Acoustic Module (without thermal and viscous losses, to reduce the computational time) with an electrostatic study and the Particle Tracing Module. A copper sleeve plate has been positioned at the middle of the duct and connected to an HVDC power source. An initial distribution of negative charged particles, based on the mesh refinement, has been considered. Thus, the behavior of this particles under the influence of the acoustic perturbation and of the applied electrical field has been observed. The particles move forward and backward along the duct due to the acoustic wave and are forced to the walls by the applied electric potential (Fig.3).
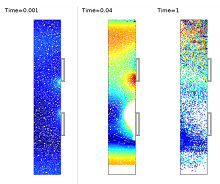
Téléchargement
- carcangiu_presentation.pdf - 2.8MB
- carcangiu_paper.pdf - 0.81MB
- carcangiu_abstract.pdf - 0.28MB