Modeling of Laminar Flow Static Mixers
Laminar flow static mixers are accurate, inexpensive fluid mixing devices that can handle a wide range of fluids and mixing proportions. They have a wide range of industrial applications, especially in the consumer product, pharmaceutical, biomedical, and petrochemical industries. A good mixing quality is obtained when the outlet of the mixer has no concentrated volumes of either mixed materials and is overall uniform. The laminar fluid mixers analyzed in this study involve multiple elements that divide and recombine the flow and elements that invert the flow to move fluid away from the external boundary layer. Accurate simulation of this type of laminar static mixers using only two-phase CFD cannot be achieved due to numerical diffusion, a computational artifact that does not reflect the actual mixing process. Veryst Engineering®, in collaboration with Nordson EFD, developed a new modeling tool for this purpose. We use COMSOL Multiphysics to perform a CFD analysis of the overall mixer performance and predict the overall flow pattern and pressure drop (see Figure 1). We then use both streamline and mass-less particle tracing (independently) to follow the path of fluid particles. Figure 2 shows the particle tracing results at an intermediate time as well as one Poincaré section which indicates the locations where particles cross a specific plane in the mixer. The streamline and particle tracing data is exported from COMSOL using the Java interface and used to compute two measures of mixing quality. The first is a coefficient of variation (CoV) which is a quantity that has a value of one, for no mixing, and zero for perfect mixing. Here, “perfect mixing” is relative to a user-controlled length scale. The second metric is a series of cross-sectional mixer images similar to Poincaré sections. These images help identify local streaks of one material that are not detected in an overall CoV analysis. We compared the results to targeted mixing experiments performed by Nordson EFD involving the mixing of two epoxy materials – a black and a white compound. These materials solidify when mixed. After solidification, the mixer is sliced into about forty sections to visually assess the mixing quality. Figure 3 shows a comparison between the experimental data and the COMSOL predictions for a Nordson® EFD mixer at three different cross-sections along the first half of the mixer. The blue colored regions in the experimental data are the mixing elements. The black and white epoxies had slightly different entry angles in the experiment and in the simulation, due to the imperfect segregation of the two epoxies prior to reaching the mixing elements. This affects the distribution of black/white epoxy at different sections along the mixer. However, fluid entry angles are known to have an insignificant effect on mixing quality. There is excellent overall agreement between experimental and simulation results in terms of identifying unmixed regions and unacceptable fluid streaks.
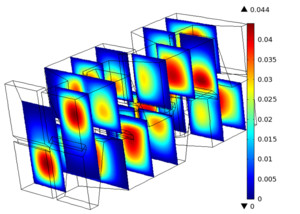
Téléchargement
- elabbasi_presentation.pdf - 1.3MB
- elabbasi_abstract.pdf - 1.23MB