Modeling of Iron Ore Reduction Above the Cohesive Zone of the Blast Furnace
The blast furnace shaft is a huge counter flow reactor in which heat and mass exchange play a significant role in its mathematical modelling. The heat exchange model is already available in COMSOL Multiphysics® via the Local Thermal Non-Equilibrium interface. This multiphysics coupling is used to account for heat transfer in porous domains where the solid and gas temperatures are not in equilibrium. This is achieved by coupling the heat equations in the solid and gas subdomains through a transfer term proportional to the temperature difference.
Flow through layered packed bed: the burden in the blast furnace shaft has a layered structure. Depending on the charging program, usually more coke is charged towards the centre and more ore towards the wall. This charging pattern has a great influence on the permeability distribution and gas flow in the burden. The coke layers have much higher permeability than ore layers since the coke particles are larger than ore particles. There are some burden layer descent models to estimate the shape of the coke and ore layers during operation with respect to the charging program and other operational conditions. The ore layers lose mass due to oxygen removal as the ore is reduced indirectly by CO. It is assumed that the particle volume stays constant and density is reduced by the increased porosity of the ore particles. The solid coke layers also lose mass as the coke reacts with CO2 to form CO by the solution-loss (Boudouard) reaction. Again, the particle size is assumed to stay constant.
Reaction kinetics models in blast furnace shaft: there are countless reactions occurring in the blast furnace shaft as the burden descends. However, many of these reactions are not directly related to the reduction process. The most important reactions are the indirect reduction of the ore by CO/H2 and the solution-loss reaction. Therefore, initially these heterogeneous reactions are modelled. These kinds of solid-gas reactions are in general modelled by the Unreacted Shrinking Core Model (USCM). The overall process proceeds through a sequence of mass transport and chemical reaction steps. The reacted solid product forms a thickening shell as the unreacted core shrinks. The transport resistance through the interface has a non-negligible influence on the overall kinetics.
The model is calibrated by laboratory experiments and operational measurements. Furthermore, it is used as an online model which computes the process state daily for changing operational conditions.
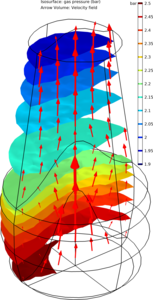
Téléchargement
- Kaymak_6441_presentation.pdf - 2.16MB
- Kaymak_6441_poster.pdf - 1.44MB
- BF_Process_Model_Conf2023_Munich.pdf - 1.75MB