- Bridging the Terahertz Gap
- Modeling the Lithium-Ion Battery
- Protection contre la Corrosion
- Modélisation des batteries
- Modélisation et Simulation dans le développement des piles à combustible
- Modélisation thermique des petits satellites
- Analyse électro-vibroacoustique d'un transducteur à armature équilibrée
Modeling Interplay Between Catalyst Performance and Microenvironment in CO2 Electrolyzers
With the anticipated effects of global climate change upon us, induced by egregious CO2 emissions, it is imperative to implement technologies to close the carbon cycle. One potential technique to do this is storing the energy from intermittent sources (e.g. solar, wind, hydro) in the form of chemical bonds, such as the electrochemical reduction of CO2 (ERC). By reducing CO2 to energetically and chemically useful products of CO2 (i.e. CO and C2H4) we can both reduce reliance on fossil fuels and mitigate atmospheric CO2 levels. However, exerting control over the ERC is challenging because of insufficient understanding of underlaying mechanisms and complexity of the overall system. First, parasitic evolution of hydrogen (HER) is always present because water serves as the proton source for ECR. Additionally, several additional variables, some not well understood, exist within the catalyst microenvironment that can also influence local CO2 concentration and ECR selectivity. The observed results of research efforts exploring new catalyst materials, can be skewed due to these microenvironment conditions. For example the relatively slow diffusivity (≈2x10-9 m2/s) of CO2 in the liquid phase can cause inefficient utilization of catalyst active sites if turnover rates are high. Therefore, it becomes imperative to understand conditions of the catalyst microenvironment while evaluating catalysts for ECR. Studies that control parameters like catalyst layer thickness or porosity in a defined cell can provide unique insight into how external conditions can tune catalyst selectivity, activity, and stability. Utilizing COMSOL Multiphysics®, we report on the successful modeling of well-defined Ag nanowire mat catalysts assembled on a gas-diffusion support (Figure 1a-c). Simple variation to the amount of casted Ag nanowires enabled variation in catalyst layer thickness which is easily implemented in the model as well. The simulation results demonstrate that large deviations in ionic concentrations (Figure 1d) exist between varying catalyst layer thicknesses which likely induce the observed substantial differences in catalyst output (Figure 1e). Further exploration of the interplay in commercially relevant electrolyzers via modeling methods can expedite optimization catalyst architecture in the industrial sector and hopefully aid in solving the global climate crisis at hand.
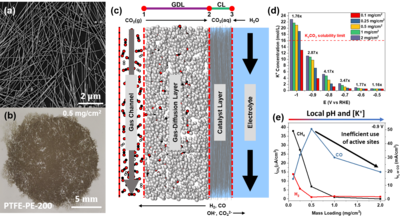