Fatigue Analysis of an Aluminum Tricycle Frame
As a sustainable urban transport system, the tricycle can represent an adaptive mobility vehicle used to transport people and bulk load. This transport system must guarantee the security of its end users, so experimental and modeling works are very useful tools in order to evaluate the mechanical performance of its frame. Finite-element analysis is usually used to fine-tune the geometry of a design that is still on the drawing board, before working models are built and tested. In a previous work a finite element model of an aluminum tricycle frame was developed by using COMSOL Multiphysics®. The static analysis of the tricycle was carried out with the Structural Mechanics Module by applying appropriate loading conditions. Stress and deformation distributions were evaluated for different combinations of loads and the analysis of the structural characteristics of the tricycle frame was carried out. A basic fatigue analysis was carried out by comparing the stress levels present in the structure to the fatigue limit of 6061-T6 aluminum fatigue limit and revealed that the long-term durability of the design is compromised. For this reason, additional fatigue simulations have been developed in order to improve the design of the tricycle, using the Fatigue module in COMSOL Multiphysics®, using the S-N curves for the material to better evaluate the number of cycles the structure might handle before fatigue cracks appear or some part of the tricycle fails. Due to the low fatigue life expected from results, 6061-T6 aluminum could represent a better choice for the tricycle fabrication and some parts of the tricycle may require being reinforced or re-designed. The computational simulations have provided useful information for improving the mechanical performance of the tricycle.
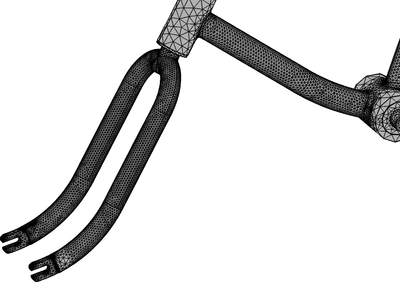
Téléchargement
- chine__poster.pdf - 0.51MB
- chine__paper.pdf - 0.72MB
- chine__abstract.pdf - 0.1MB