Direct FEM Ampacity Calculations for Submarine and Underground Power Cables
High-voltage power cables are vital components of power transmission systems. Submarine cables are critical power carriers between offshore wind farms and onshore ac grids. Moreover, underground cables are generally preferred over overhead installations in land applications, owing to environmental, aesthetic and reliability reasons [1].
To ensure the safe and reliable operation of power cables, it is crucial to estimate their ampacity most accurately and efficiently. The cable ampacity is dictated by the maximum operating temperature that the insulation can withstand without getting downgraded. For cables insulated with cross-linked polyethylene (XLPE), the thermal limit is typically set to 90°C. In practical applications, power cable loss and ampacity calculations are commonly performed using the IEC 60287 standard. Specifically, IEC 60287-1-1 provides the necessary formulas for the determination of the conductor resistance, sheath, dielectric and armor losses in a three-phase cable circuit [2]. These formulas are utilized by the proposed thermal circuit model in [2], which enables the computation of the permissible cable ampacity, by estimating the thermal resistances of the non-metallic parts of the cable. This model renders the thermal problem one-dimensional, as it assumes radial heat dissipation within the cable. However, this assumption does not entirely hold, especially in the case of three-core (3C) separate lead (SL)-type submarine cables, where the close physical proximity of the three cable cores leads to the inevitable distortion of their temperature fields [3]. Furthermore, in finite-element method (FEM) models, the heat transfer equations are solved for temperature, which occurs as an output. Therefore, it is not feasible for someone to directly calculate the cable ampacity in the existing FEM models and, consequently, repetitive runs, including many trials, are required for this purpose.
In this paper, a two-dimensional (2D) FEM thermal cable model is developed, using the COMSOL Multiphysics® software. The purpose of this model is to compute the ampacity of the investigated cable in a direct manner, given the predetermined upper thermal limit. While losses are imported according to the IEC 60287-1-1 standard, the use of the 2D FEM solver allows for the inclusion of heat proximity effects in the analysis. To effectively determine the cable ampacity, two approaches are adopted: first, a direct ampacity method is employed, by pre-assuming the hottest cable core and assigning a Dirichlet condition on that; subsequently, a more generic method, making use of the Οptimization Μodule of COMSOL Multiphysics®, is employed and used to validate the direct ampacity method. Both submarine and underground cable designs are examined. The results of this study are compared with respective thermal calculations, which are obtained via commercial software implementing the IEC 60287 standard. This comparison is performed in terms of ampacity as well as thermal resistance estimations, showcasing the inadequacies of the IEC 60287 method.
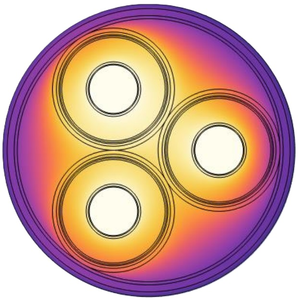
Téléchargement
- Manuscript_KBitsi.pdf - 0.45MB
- Bitsi_4621_poster.pdf - 0.36MB