Comparison of Pipe Flow vs. CFD Module for Homogeneous Liquid Delivery to a Tank in a Cooling Reactor
We consider the fluid dynamics problem of homogeneously filling a large tank by multiple inlets fed from a piping system. Suitable pipe geometries must be chosen so that the volume flow is constant for all inlets. In this work, we compare both for a piping system as depicted in fig. 1: A main pipe is feeding four secondary pipes that deliver the liquid to the tank. The boundary conditions are the inlet velocity vin at the main pipe entrance and p=patm at the rising pipe ends 1-4.
The target is to design a pipe systems that leads to homogeneous outflow velocities at the rising pipe ends 1 to 4. For each simulation, we calculate the homogeneity as H=(vmax(1-4)-vmin(1-4))/v_average(1-4).
In order to assess advantages and disadvantages of the Pipe Flow simplifications in COMSOL Multiphysics®, we perform comparative simulations and record mass conservation, convergence behavior, memory allocation and computing time. This will allow us to determine the requirements (laminar / turbulent flow, Re number, pipe geometry, adapted loss factors) for successful Pipe Flow Module application for this problem.
For the Pipe Flow Module calculations, we have to choose loss factors Kmain and Kside for the T junctions as well as K for the 90° bend at the rising pipe 4. Also, we use round geometry of the pipes without surface friction and Churchill friction model with vanishing surface roughness. The CFD model requires much less parameters as the real geometry is entered without using any lumped loss factors e.g. Stationary studies are conducted with varying pipe geometries and inlet velocities vin. The results are average pipe velocities (Pipe Flow) and local flow velocities (CFD) that are used to test for global mass conservation (total volume inflow and outflow) and to calculate homogeneity H as defined above.
The first simulations are conducted using laminar flow conditions (Re
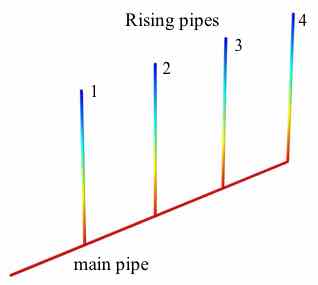
Téléchargement
- leis_poster.pdf - 0.39MB
- leis_abstract.pdf - 0.03MB