Carbon Steel Pipeline Wall Thickness Measurement Using Pulsed Eddy Current Technique
Carbon Steel pipes are used as feeder pipes in Pressurized Heavy Water Nuclear Reactors for carrying the coolant from the inlet headers to the coolant channel and again from outlet of the coolant channel to the outlet headers and are part of the Primary Heat Transport (PHT) System of Reactor. It has been observed that these feeders suffer from Flow Accelerated Corrosion (FAC) at the bends and elbows. It is required to design a Pulsed Eddy Current (PEC) based sensor to monitor the feeder pipeline thinning during bi-annual shutdown of the reactor as a part of In-Service-Inspection (ISI). COMSOL Multiphysics® software has been used to optimize the sensor size, dimension and structure and was used to simulate the response of the sensor. The resolution of the sensor in terms of minimum wall thickness variation between two test specimens was also carried out.
Use of COMSOL Multiphysics®: The AC/DC Module present in COMSOL Multiphysics® has been used for our analysis. A 3-D model was developed for this purpose consisting of the sensor as well as the test specimen, which was approximated by a flat surface as the contact area between the specimen and sensor is very less. The sensor consists of an Excitation coil and an internal pick up coil sensor of copper. A ferrite core has been used to concentrate the magnetic flux. Coarse Tetrahedral Meshing was used for the model. The excitation waveform was the rect(t) function with an ideal switching time of 1e-6 sec and an on time of 10 ms. Eddy Current is produced on the specimen surface as an effect of induced voltage due to change in magnetic flux during transition from ON state to OFF state & vice versa of the Pulsed excitation waveform. The Voltage developed in the receiver coil is due to the net vector difference of the magnetic field of the Excitation coil and that due to the Magnetic field of the eddy current. It is seen that the voltage produced in the Receiver decays off when the pulse is switched off. The slope of the decay waveform is a function of the thickness of the specimen. By plotting logarithm of the received voltage against time the variation between two thicknesses can be easily found out. Decay Coefficient, inverse of the decay slope is defined which increase with thickness of the specimen. Moreover the effect of variation in Lift-off which is the distance between the Sensor and the test specimen on the received waveform was also studied.
The model was able to differentiate between thickness variation of about 0.5mm. Moreover it was also found that if the Lift-Off is between 0.5mm then there is no effect in the characteristics of the received waveform.
COMSOL Multiphysics® software was successfully used to model Eddy current sensor for Carbon Steel Pipeline Wall Thickness Measurement. The simulation results obtained from the model are in line with the experimental results.
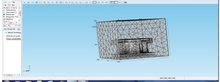
Téléchargement
- roy_presentation.pdf - 2.07MB
- roy_poster.pdf - 0.33MB
- roy_abstract.pdf - 0.13MB