- Bridging the Terahertz Gap
- Modeling the Lithium-Ion Battery
- Protection contre la Corrosion
- Modélisation des batteries
- Modélisation et Simulation dans le développement des piles à combustible
- Modélisation thermique des petits satellites
- Analyse électro-vibroacoustique d'un transducteur à armature équilibrée
Advanced Particle-Based 3D Modeling of Fuel Cell Electrodes
Fuel cells are electrochemical devices which produce electricity from renewable and clean resources, such as hydrogen. Their large-scale exploitation is expected to impact positively our approach to use electric energy in vehicles, buildings and other portable/stationary applications. However, the degradation of the porous electrodes remains a challenge and advanced modelling is required to understand the fundamentals of efficiency loss. In this study, we used COMSOL Multiphysics® 5.2 to simulate the transport and reaction phenomena within the real 3D geometry of a solid oxide fuel cell electrode. The complex electrode microstructure, comprising two conducting solid phases and a porous phase, was reconstructed with focused ion beam-scanning electron microscope tomography with a resolution of 30 nm. The microstructure was meshed with Simpleware ScanIP® and exported as a Nastran file comprising more than 30 millions mesh elements. The mesh was imported in COMSOL Multiphysics® 5.2, where different physics were applied by using the General Form PDE interface: electron conduction within the metallic phase, ion migration in the ceramic phase and gas diffusion in the porous phase. The electrochemical reaction source term, converting chemical species into charged species, was assumed to occur at the shared edges of the three phases, which were selected via Boolean operations on the meshed geometry. The steady-state solution was obtained by running the model in a cluster computer, requiring more than 150 GB of RAM. The distribution of field variables was extracted on the mesh Gauss points and then interpolated to a regular 3D grid by using an in-house MATLAB® code. This procedure allowed us to advance for the first time the complex statistical distribution of the current transferred by each individual particle within a fuel cell electrode. The analysis revealed an inhomogeneous current distribution at the particle level, with more than 30% of particles which are underutilised and just a tiny fraction of particles which convert more current than average. These results were confirmed also in synthetic microstructures, allowing for the detection of hot spots where Joule heating can trigger degradation process. This insight opened the opportunity to re-think about the particle arrangement in porous microstructures and to suggest novel design strategies to optimise the electrode architecture and thus minimise the occurrence of degradation spots. The extension of the approach to lithium-ion and redox-flow batteries is currently under development. In addition to the scientific and technological implications for fuel cell manufacturing, the study offers a fresh perspective on the best practices used in handling big and complex 3D models in COMSOL Multiphysics® in terms of compatibility with partner meshing software, cluster platforms and workflow optimisation from the geometry to the results.
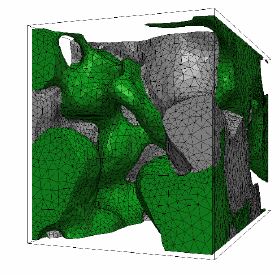
Téléchargement
- bertei_presentation.pdf - 4.15MB
- bertei_abstract.pdf - 0.04MB