Additive Manufacturing of Metal Matrix Composites
Laser cladding is an additive manufacturing process, where a laser beam creates a melt pool, into which powder is fed from a powder nozzle. Due to the feed motion of the laser beam and the powder nozzle relative to the workpiece, coatings and 3D parts can be deposited, which consist of numerous overlapping weld beads. When carbide particles such as titanium carbide particles are mixed into the metal powder, the process results in highly wear resistant metal matrix composite (MMC) coatings, which are commonly applied in several heavy duty applications, for example on mining tools. As the carbide particles are often different in density compared to the metal matrix material, they tend to accumulate on the melt pool surface or on the bottom, respectively. In order to achieve a homogeneous carbide particle distribution, suitable process parameters have to be found. A process simulation supports this parameter optimization and improves the process understanding. COMSOL’s Particle Tracing module allows investigating the behavior of the carbide particles inside the melt pool. The melt pool is initially simulated in consideration of heat transfer, laminar melt pool flow, surface tension and the Marangoni effect. The powder jet characteristics such as the powder jet diameter, which are required as input data for the melt pool simulation, are obtained from a separate simulation of the process gas flow and powder particle flow from the powder nozzle to the workpiece surface. The latter simulation additionally provides insight into the composition of the shield gas atmosphere with regard to the oxygen content as the transport of concentrated species is considered. The final results show, that the melt pool flow has only a minor effect on the carbide particle distribution and the simulation is able to predict the homogeneity of the carbide particle distribution. Moreover, general recommendations for the process parameters and for the carbide particle size can be derived.
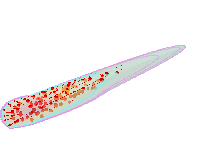
Téléchargement
- wirth_presentation.pdf - 2.77MB
- wirth_poster.pdf - 1.63MB
- wirth_abstract.pdf - 0.02MB