Continuous Mixer
Application ID: 80631
Continuous mixing is used in process equipment to mix components in a single pass. Compared to batch mixing, this operation has the advantage that the tank filling and emptying steps are eliminated, implying that the process can be run without interruptions. A disadvantage of continuous mixing is that the time that the material spends in the mixer, the residence time, is not constant. The residence time is to a large extent dependent on the details of the mixer construction and the operation. Parameters that affect the residence time are for example the position and speed of the impeller and the feed rate at the inlet.
In this model a tank with an asymmetrically positioned impeller is modeled. The tank and impeller geometry are defined using parts from the Mixer Module Parts Library.
A liquid is continuously fed to the tank through an inlet near the top. The liquid then exits through an outlet at the bottom. The turbulent flow field resulting from the impeller agitation is solved for using a frozen rotor analysis.
The model shows how to visualize the mixing, and compute the residence time distribution using particle tracing. A pulse containing 50000 massless particles is injected and tracked as it flows through the mixer. The residence time distribution is computed by counting the number of particles that have reached the outlet at a certain time.
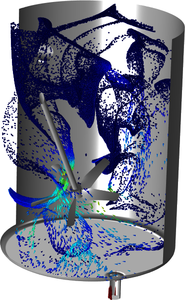
This model example illustrates applications of this type that would nominally be built using the following products:
however, additional products may be required to completely define and model it. Furthermore, this example may also be defined and modeled using components from the following product combinations:
- COMSOL Multiphysics® et
- Module Mixer et
- Module Particle Tracing et
- soit le Module CFD, ou Module Heat Transfer et
- soit le Module CFD, ou Module Polymer Flow
The combination of COMSOL® products required to model your application depends on several factors and may include boundary conditions, material properties, physics interfaces, and part libraries. Particular functionality may be common to several products. To determine the right combination of products for your modeling needs, review the Grille des Spécifications and make use of a free evaluation license. The COMSOL Sales and Support teams are available for answering any questions you may have regarding this.