Continuous Casting: Optimizing Both Machine and Process with Simulation
N. GrundySMS Concast, Switzerland
The process of continuous casting has transformed steel production, saving valuable resources while improving steel quality and process efficiency. Continuous casting involves carrying molten refined steel to a caster. There, water-cooled copper molds are used to form steel strands that are cut and then cooled. High-quality steel production requires minimizing the presence of non-metals in the steel, improving the microstructure, and maintaining even composition by reducing the segregation of alloying elements. Engineers at SMS Concast, a Switzerland-based company specializing in continuous casting technology, have used COMSOL Multiphysics to model mechanical deformations, the fluid motion present as molten steel flows into the molds, and the cooling process. Using their simulations, they have studied coupled physics that would be impossible to model otherwise – such as the heat transfer during initial solidification and the electromagnetic fields generated by stirring equipment.
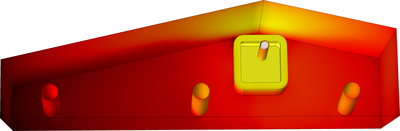
Téléchargement
- SMS_Concast_CN2014.pdf - 0.25MB