Rolling Contact Fatigue in a Linear Guide
Application ID: 35361
When a linear guide is loaded above the manufacturer's specification limit, one concern is whether the contact loads will introduce fatigue spalling. In this system analysis, the entire guide has been analyzed and the mostly damaging contact load has been identified to occur on a rail raceway. Since spalling is initiated by a fatigue crack on the subsurface level, a fatigue evaluation based on the Dang-Van model is performed.
The fatigue evaluation of a moving contact load on a curved surface requires a controlled mesh. The elements' sizes must be small enough to correctly resolve the contact pressure on the surface. And, as we are analyzing a rolling contact, the contact pressure is dynamic along the surface so that the entire area of the traveling contact must consist of small elements. Moreover, the largest shear stresses in a contact analysis are found on the subsurface level, so that a fine mesh is also required throughout the depth of the model.
A technique for handling such a challenge is demonstrated in this model.
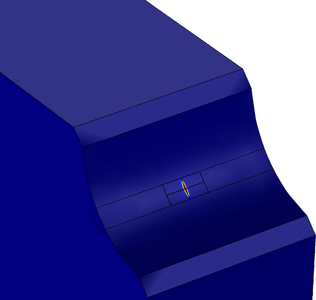
This model example illustrates applications of this type that would nominally be built using the following products:
however, additional products may be required to completely define and model it. Furthermore, this example may also be defined and modeled using components from the following product combinations:
The combination of COMSOL® products required to model your application depends on several factors and may include boundary conditions, material properties, physics interfaces, and part libraries. Particular functionality may be common to several products. To determine the right combination of products for your modeling needs, review the Grille des Spécifications and make use of a free evaluation license. The COMSOL Sales and Support teams are available for answering any questions you may have regarding this.