Three-dimensional time resolved fluid mechanics simulation of an EWOD-driven micropump
This work reports how an EWOD-driven micropump is simulated using COMSOL Multiphysics®. Electrowetting-on-Dielectrics (EWOD) is frequently used technique to manipulate liquids on small scales. With the help of the EWOD effect and the use of topological optimized tesla valves, a pump can be manufactured that does not require any moving components [1]. The pump chamber contains a few hundred thousand of deep-etched cavities in silicon (see Figure 1). A hydrophobic layer is applied on top of an intermediate dielectric layer on the surface of the cavities to force the liquid into the Cassie-Baxter state. By applying an alternating voltage between the liquid and the heavily doped silicon, the wetting properties of the liquid change, and the liquid-vapor interface is periodically and reversibly deflected inside the microcavities.
For the simulation, an analytical model for the deflection of the liquid-vapor interface inside the microcavities is used and combined with a time dependent three-dimensional flow simulation using the COMSOL Multiphysics® CFD-Module to determine the frequency dependent flowrate of the micropump. The analytical model is based on the work of MATSUMOTO and COLGATE [2]. From the analytical model a voltage and volume dependent pressure response curve of a single cavity is determined. This pressure response curve is used as a boundary condition on the inlet for the fluid mechanics simulation. To ensure that the limited volume stroke of the cavities is modelled correctly, the pressure difference on the inlet is linked to the overall volume difference at the two outlets of the micropump via two additional global differential equations.
To keep the simulation time short and the amount of data small, a chirped voltage signal is used to excite the micropump. The frequency is increased linearly from 0 to 400 Hz over a period of six seconds. Afterwards the spectrogram of the difference of the flow rates at the two outlets is calculated, leading directly to the frequency dependent flow rate.
The fluidic properties of the micropump, like the maximum pump pressure or the flowrate, can be tailored by varying the geometry of the cavities, the type and thickness of the dielectric intermediate layer or the hydrophobic coating. Simulation results for different sets of parameters are presented and discussed.
[1] Hoffmann, M.; Dittrich, L.; Bertko, M.: Mikropumpe zur Erzeugung einer Fluidströmung, Pumpensystem und Mikro-kanalsystem. WO 2012/084707 A1, 28.06.2012
[2] Matsumoto, H.; Colgate, J.: Preliminary investigation of micropumping based on electrical control of interfacial ten-sion. In: IEEE Proceedings on Micro Electro Mechanical Systems, An Investigation of Micro Structures, Sensors, Actua-tors, Machines and Robots. (1990), DOI 10.1109/MEMSYS.1990.110258
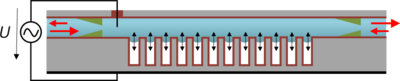
Téléchargement
- Comsol_2020_Paper_SB.pdf - 0.7MB
- 20200919_COMSOL_SB_slides.pptx - 5.74MB