Simulation of Spiral-Tube Heat Exchangers in COMSOL Multiphysics® Software
A frequently occurring geometry for heat exchangers is that of a long tube wound into a helix or spiral around a core volume. There is to be heat exchange between the tube and the gases (or solids) in the core. However, the length scales of these two parts of the geometry are very different, thus complicating the interface between the tube and the core processes.
Usually, the tube is too long for direct numerical modeling. Therefore, in the present work, we use an axis-symmetric numerical model of the core and link it to analytical equations for the tube. In this way, radial boundary conditions at the core perimeter become the driving force for the thermal process in the tube; at the same time, the results of the analytical integration in the tube provide boundary conditions for the core. Also, it is shown that there is enhanced convective heat transfer in the curved tubes, compared to straight tubes.
To facilitate the interface conditions, COMSOL Multiphysics® software is used on a detailed tube geometry section to derive a shape factor, which maps the tube perimeter temperatures on to a plane surface over the pitch of the helix. Examples are provided where the spiral, or helix, consists of metal and of quartz glass. It is shown that both convection and radiation are significant in high temperature problems.
It is common practice in such designs to provide gaps between the coils to allow radiation to reflect and reradiate from a ceramic back surface. This provides direct radiation to the back side of the tubes but reduces the tube length and hence the total surface area.
The benefit of such practices depends on the behavior of the tube wall in conducting heat to the back side of the tube and the internal heat transfer rate. The different thermal conductivities of the quartz and metal tubes show the effect of the tube properties. Other important effects are on the heat loss which is lower for a tightly coiled spiral and the pressure drop which is lower for a loosely wound spiral because of the shorter tube length.
The use of the integrated modeling for such complex behavior can lead to significant benefits in design optimization, particularly as the external heat transfer coefficient on the tubes is frequently much lower than that on the inside.
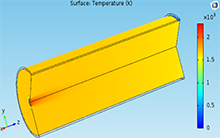
Téléchargement
- lund_presentation.pdf - 0.45MB
- lund_abstract.pdf - 0.02MB