Simulation of Magnetic Flux Distribution of Stator and Rotor Coil of Superconducting Air Cored Wind Turbine Generator using COMSOL Multiphysics
Wind energy is one of the fastest growing renewable energy sources for electricity generation over the past decade. The offshore installation of large-scale wind farms draws huge attention because of better wind profile. Direct drive synchronous wind turbine generators are now a global demand for light weight, compact, large scale wind turbine generators. Among various approaches in designing direct drive superconducting wind turbine generators, a comparatively new design (Figure 1) having both axial and radial air gaps between stator and superconducting rotor winding is selected for simulation work. It has the advantages of uniform stress and magnetic force around the circular coil. Elimination of gear box leads to light weight of the wind turbine generator. This paper deals with the simulation of magnetic flux distribution of stator and rotor coil of the same using the sliding mesh tool of COMSOL Multiphysics. The model geometry of the wind turbine generator mentioned earlier was drawn using 3D CAD tool of COMSOL Multiphysics. After declaring the global and local parameters, the magnetic and electric fields (mef) is chosen for setting the physics of the model in AC/DC module. It is followed by the proper assignment of material properties of the coils and core. To implement the rotational effect of the rotor coil on the stator magnetic field, sliding mesh concept is used. Parametric sweep is incorporated in study portal, which evaluates field distribution of the model for every angular position of the rotor with respect to the stationary axis and stores the results. Time dependent study was performed thereafter. Physics controlled mesh was directed with extra fine setting (figure 2,3). Total number of elements was found to be 1029920. Flux distribution in the rotor coil is realized here using volume plot of magnetic flux density (normal). The simulated magnetic field is distributed almost uniformly throughout the outer part of the stator and the same varies gradually with the distance from the centre in each coil (figure 4) of the rotor. Some animations from different angle are captured in the post processing. The simulation software COMSOL Multiphysics has been used to simulate a parametric model of a circular superconducting air core coil of direct drive off sore wind turbine generator. The solution has been efficiently computed using the built-in tools and solvers of COMSOL Multiphysics. Sliding mesh technique incorporating parametric sweep gave the realistic effect of rotation of the rotor with respect to the stator on flux distribution. In summary, 3D model geometry has been efficiently constructed in 3D CAD tool of COMSOL Multiphysics and it is found to be a very flexible and efficient tool for numerical field computations.
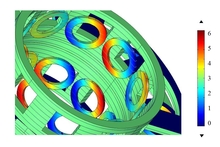
Téléchargement
- hazra_presentation.pdf - 0.81MB
- hazra_paper.pdf - 0.7MB
- hazra_abstract.pdf - 0.21MB