Simulation of Fluid Flow in an Artificial Soiling Device
Solar systems are used around the world, especially in sunny and dry regions, to convert radiation energy from the sun into electricity or heat. Soiling, as dust deposition onto surfaces is commonly called, hinders this conversion of the solar energy by blocking of the incidenting light. Dust is basically carried by wind. In this study the turbulent fluid flow mechanics in a closed artificial soiling system are modelled with COMSOL Multiphysics® to simulate the actual transport of dust particles as it is happening in the closed system.
A simplified approach to simulate the soiling process can help to understand the interactions of environment, particle and surface better. So far to the knowledge of the authors only few simulation studies have been conducted that analyze the physics of the soiling process. This study sets the framework and explains the turbulent fluid flow that occurs during the soiling process in a closed system, which can be validated easily.
Finite Element Method (FEM) simulations of an in-house developed artificial dusting device are created using COMSOL Multiphysics® in 2D and 3D. The results of the simulation can be verified with fluid flow experiments conducted with the artificial dusting device.
Fluid flow experiments conducted with the artificial dusting device were compared with the simulation created in COMSOL Multiphysics®. The turbulence model is the foundation for the understanding of the fluid mechanics involved in this simulation. This turbulence model adds three equations to the standard Navier-Stokes equation to be able to account for turbulence.
The turbulent viscosity defines how the turbulent behavior of the fluid will be. This formulation of the turbulent viscosity relies upon two additional transport equations to define k and epsilon to supplement what the Reynolds Averaged Navier-Stokes equation cannot express. For the numerical simulation a 2D and 3D model were created to reflect the set-up seen in Figure 1, and compared to fluid flow experiments. The quality of the mesh, the wall resolution, stabilization methods, turbulence models and characterization of the fluid flow were all taken into account while developing the simulation.
The results show the fluid flow as it streams through the artificial soiling device at three different inlet velocities (Fig. 2). Those inlet velocities represent commonly occurring wind speeds in the desert environment of Fraunhofer ISE outdoor test field in the Negev Desert and being used for the dusting device. It is shown, that with the aid of COMSOL Multiphysics®, a simulation of the fluid flow is comparable to the results observed from the in-house artificial dusting device. The flow was successfully replicated and pre-defined dust particles can be introduced into the stream.
The results of this simulation very well match the results of the experimental results from the artificial dusting device and hence are validated. This proves that through the creation of the numerical simulation, the physics of the fluid flow through the experimental set-up is now understood in terms of dust particle carriage. A first step towards a deeper understanding into the physics of soiling was achieved and can now be transferred to a macro-scale outdoor test field.
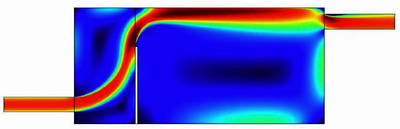
Téléchargement
- klimm_presentation.pdf - 1.48MB
- klimm_paper.pdf - 0.29MB
- klimm_abstract.pdf - 0.14MB