- Bridging the Terahertz Gap
- Modeling the Lithium-Ion Battery
- Protection contre la Corrosion
- Modélisation des batteries
- Modélisation et Simulation dans le développement des piles à combustible
- Modélisation thermique des petits satellites
- Analyse électro-vibroacoustique d'un transducteur à armature équilibrée
Simulation of a Bimetallic Alloy Cooling Process*
Bimetallic mechanical parts made of steel and bronze combine in an optimal manner the mechanical properties of the steel and the excellent anti-friction characteristics of the bronze. These properties make applications possible in various high-tech domains such as aviation, energy and transports industries. In such components, one or more surfaces of the steel are covered with a thin layer of bronze. The steel-bronze interface features a zone of intermetallic diffusion of between 3 and 5 microns. This ensures perfect adhesion and, in every case the mechanical properties of the interface are superior to those of bronze itself. Steel and bronze are linked in an inseparable fashion to form one part. The parts are produced by a process of gravity casting of bronze onto steel. After casting, a major phase of the production is the cooling. After casting and cooling, the parts are re-machined. The way of cooling is fundamental to get a steel-bronze interface with controlled shrinkage and without cracks. In the standard production process cooling rings and tubes are used to pulse air on the part to be cooled (Fig 1). The temperature, the orientation and the velocity of the air flow influence the evolution of the solidification front in the bronze. A bad forced cooling will lead to a high level of shrinkage and cracks near the steel-bronze interface. The cooling process is usually well known for parts with standard geometries. However, there is an increasing demand from the industry for parts with complex shapes. In such a case the tuning of the cooling process may not be easy. This is where multiphysics simulation can help.
In this paper we present a Comsol Multiphysics simulation model of a bimetallic alloy cooling process. The solid bronze is placed in the hollowed part of the cylinder-shaped steel and covered with another steel plate on top of the bronze. The system is placed directly in an oven to be heated to 1020 °C. When this temperature is reached, the bronze is liquid and the steel solid. The system is removed from the furnace and placed in the cooling device. A thermal isolation strip is added on the upper limits of the steel. The system, surrounded by an air domain, is then cooled by two cooling rings and a central tube. The model is using the Turbulent Fluid Flow interface of the CFD module, the Heat Transfer in Fluids and Solids interface of the Heat-Transfer module and the Thermal-Structure interaction interface of the Structural Mechanics module. The phase change in the bronze and the thermal radiation are considered. The residual stresses are computed with the Ramberg-Osgood model and the level of shrinkage is estimated by the implementation of the Niyama criterion. The simulations also allow to track the solid fraction and the solidification front (Fig.2), to understand the cooling fluid flow distribution around the part and the temperature distribution (Fig. 3). The simulation results with Comsol Multiphysics are compared with experimental measurements with a good level of agreement.
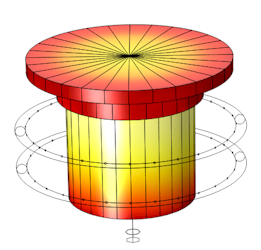
Téléchargement
- paper_rozsnyo_hofmann_lienard_comsol_2024_florence.pdf - 1.25MB
- masserey_9501_poster.pdf - 0.43MB
- 2_alexandre_masserey.pdf - 0.77MB