Simulation Driven Design and Verification of Flow and Heat Exchange Optimized DMTA Measuring Systems
The Anton Paar Modular Compact Rheometer MultiDrive series allows DMTA measurements over a broad range of temperatures, from -160°C to +350°C, thanks to the CTD600 convective temperature chamber. A novel set of measuring systems has been simulated designed and verified with support of COMSOL® simulations, for all the supported geometries, in order to achieve low temperature gradients in the specimens. A typical application for DMTA measurement is the testing of specimens with a three-point bending procedure, the upper and lower measuring systems interact thermally with the specimen and the development aimed at reducing the cold spots.
During the design phase, COMSOL Multiphysics® has been used to evaluate different geometries and guide the actual design of the aerodynamic elements, helping in achieving the goal of a thermal and flow efficient measuring system: a fast exchange between design and simulation was possible thanks to LiveLink™ for PTC Creo Parametric™. The Heat Transfer Module allowed the study of all heat transfer mechanisms occurring in the convective chamber and the multiphysics interface with the CFD Module completed the knowledge of the measuring setups.
Visualization of results in terms of temperature and streamlines highlighted the interaction between aerodynamics and heat exchange, guiding the design. The achieved temperature gradient was then trimmed for all the different specimens of 10, 20 and 40mm, allowing consistent testing parameter with different testing specimens. The chosen design was then verified, after production of prototypes: the experimental campaign was set up with help of virtual specimen in the simulation model and the model was found to be consistent with the expected values.
In particular, a temperature sensing dummy was defined for the different lengths of the three-point bending, in order to validate the model and verify the temperature gradient during testing COMSOL Multiphysics® allowed a faster cooperation between designers, testing and simulation engineers, allowing a simulation driven design, which could be validated by means of intensive testing campaign.The final result is then a series product which can reliably be used in different testing condition, and a digital twin for the simulation engineers, allowing future customized solution to be consistent with the original development.
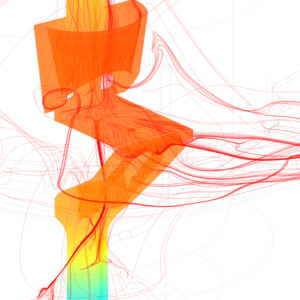
Téléchargement
- D'Uffizi_4491_poster.pdf - 5.19MB