Processing Tank Flow Mechanics and Design for Next Generation Advanced Chip Scale Packaging
Experts in the industry are seeing glass substrates as a promising alternative material for interposers, particularly for heterogeneous packaging such as 2.5D or 3D packages [1]. Recently, Intel revealed that they have developed one of the industry's first substrates specifically tailored for advanced packaging of the next generation [2,3]. Using Through-Glass Vias (TGV) on glass panels is a crucial technique for creating 2.5D/3D packaging solutions. Glass substrates offer advantages such as rigidity, flatness, and thermal stability, enabling a tenfold increase in interconnect density. To create via holes, laser techniques are initially used, followed by wet etching to achieve the proper diameter. Then, metal and thin layer deposition is carried out through various methods, including electroless plating, electroplating, PVD, and CVD. This paper focuses on optimizing wet tank processes to achieve the best planar uniformity using the methods mentioned above. A typical wet tool for processing glass panels involves multiple steps, with each step taking place in a separate tank. The substrates are immersed in different chemical solutions one after the other in a linear fashion. The process must maintain uniformity so that deposition or etching occurs similarly at various parts of the panel. The standard size of the panel is 510x515mm, and multiple glass substrates are usually processed simultaneously. Therefore, a panel carrier must be designed for successful high-volume manufacturing. This carrier should allow for practical automated loading and unloading of panels, as well as the locking of panels and transportation of the carrier between various tanks. When a carrier containing multiple panels, locking pads, and mechanisms is lowered inside a tank, it can remain stationary or move up and down or side to side, which enhances mixing. Bubbles can also be introduced for the same purpose, thus creating a more effective mixing process. This study aims to examine the flow velocities between the panels, the carrier walls, and the tank walls in stationary up and down positions. The flow field is obtained by numerically integrating the incompressible Navier-Stokes equations using COMSOL software packages for computational fluid mechanics (CFD). Both laminar and turbulent flow options will be evaluated, combined with chemical etch reactions and multi-physics electroless processes. The overflow tank comprises three primary fluid components: the lower distribution area, a showerhead-like platform, and the main tank where the carrier and panels are located. The lower distribution area has a higher velocity turbulent flow, while the showerhead consists of thousands of orifices and is simulated as porous media. Flow resistance in the platform is calculated using the Darcy-Forchheimer approximation, and coefficients are obtained separately by directly solving the flow through a smaller segment of orifices. The overflow tank is a crucial component of the sparger system, and it usually has a capacity of 150-300 liters. The tank undergoes 15-20 complete volume changes every hour. The mass flow rate is typically between 30-80 liters per minute, which results in average velocities of 3-5 mm/s. As a result of this flow rate, the areas between the panels are usually laminar, while larger open volumes in the tank tend to be turbulent. To achieve an optimal design trade-off, we study the interplay between porous resistances, showerhead planar coverage, carrier-to-platform distance, carrier-to-free surface distance, carrier-to-wall gaps, and distances between individual panels. Our approach involves creating a custom flow field in the sprayer tank that is as uniform and unidirectional as possible, particularly in the areas between the panels. We design the individual tank and carrier components in a way that avoids the formation of stagnation zones or zones with backflow. This design ensures shorter residence times, which is critical for the effectiveness of the sparger system. The convective process dominates chemical transport in the boundary layer. Therefore, our findings apply equally to wet chemical etching of TGV vias (using NaOH) or electroless processes.
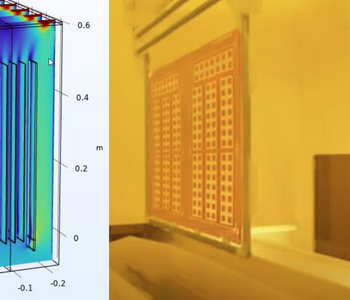