Process simulation of Directed Energy Deposition process using COMSOL Multiphysics®
The process-induced deformation in the DED fabricated part is a critical issue to the scaling of the technology. Currently, an inefficient and expensive experiment trial-and-error approach is utilized to tackle this issue, however it is not feasible for large parts. Researchers have therefore focused on modeling and developed several modeling strategies. Computation time remains a roadblock with these traditional models. Hence, almost no work is available in the literature focusing on large-part simulation. In the present paper, firstly the author develops traditional DED models on COMSOL Multiphysics® to highlight their limitations for large part simulation. The author then proposes a time-efficient simplified model capable of accurately simulating large parts. Heat transfer in Solids, Solid mechanics, and Events physics are combined to model the thermomechanical response of the part fabricated by the DED process. The numerical models provide detailed insight concerning the temperature evolution and deformation in the DED part. The numerical models are successfully validated with experimental data obtained at Irepa Laser. The proposed model yields better results when compared with traditional models in terms of computation speed and accuracy. Finally, the proposed model accurately simulates an industrial part within a few hours of computation time.
Keywords: Directed Energy Deposition; thermomechanical modeling; meso-scale, macro-scale, efficient thermal cycle; inherent strain,
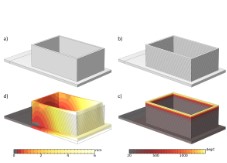
Téléchargement
- vaibhav_comsol.pdf - 0.78MB
- 4_vaibhav_nain.pdf - 6.08MB