Optimizing the Design of Polymer based Unimorph Actuator using COMSOL Multiphysics
Cantilever beam-type transducers have been in great demand and explored widely in the recent years, typically in thin film form because of their sensor and actuator applications. The piezoelectric cantilever is the most preferred structure employed in technological applications. Depending on the required flexural motion and sensitivities, these piezoelectric cantilevers can be used in unimorph, bimorph and multilayer configurations. Compared to bimorph and multilayer structures, unimorph cantilevers are in wide use for their simple structure and easy assembly. Their applications include microfluidics control and delivery, micropumps, ultrasonic liquid ejectors. They are also being utilized for applications such as microfluidics sprayers for DNA mass spectroscopy and many more applications are still emerging, Further, polymer based unimorph and bimorph configurations have attracted major interest because of their demands in aeronautic, aerospace and industrial applications. Aeronautical applications require flexibility, durability and light weight material with high degree of robustness. The piezoelectric ceramics are brittle and heavier in nature and many of these attributes are provided by piezoelectric polymers. PVDF is mostly preferred polymer. A unimorph cantilever beam consisting of a piezoelectric polymer like PVDF with a non-piezoelectric layer coating of different materials on the other side is considered for the study. The fabrication of such cantilever beam is an expensive affair, hence, it is important to optimize the device parameters before the actual fabrication of beam and hence, this piezoelectric cantilever is designed and its response with the electrical signal is simulated with the help of COMSOL Multiphysics software. Figure 1. Variation in tip deflection of the unimorph cantilever beam with the thickness of different substrate materials. It is well known that the tip deflection of a unimorph cantilever is dependent on its geometrical dimensions and material properties etc. Hence, it becomes necessary to optimize the device dimensions in order to achieve maximum deflection in a microactuator. In this work, an attempt has been made to study the effect of device parameters on the deflection of the unimorph cantilever. An optimum design of the cantilever can be found by adjusting parameters and device dimensions. It is concluded that the thickness of piezoelectric layer plays a dominant role in determining the tip deflection of the beam compared to the thickness of nonpiezoelectric layer. The lesser the thickness of the piezoelectric layer, higher is the deflection. The optimum value obtained for the thickness of PVDF is 5?m. It is also seen that the maximum tip displacement produced is for Si3N4 layer as compared to polysilicon and stainless steel being chosen as passive layer as is shown in figure 1. The design parameters are optimized for achieving maximum tip deflection and their role on the tip displacement will be discussed.
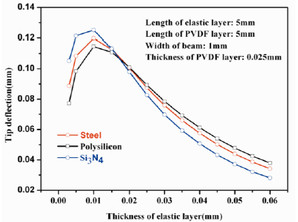
Téléchargement
- tiwari_presentation.pdf - 1.16MB
- tiwari_paper.pdf - 0.41MB
- tiwari_abstract.pdf - 0.14MB