Optimization of Product from a Segregated Reactor via a Hybrid Modeling Approach
In the field of chemical reaction engineering chemical kinetics and fluid dynamics are described by various mathematical approaches. Such tools help to shorten the time-to-market of novel products and processes. Thanks to the continuously improving computation power, it is possible to consider the kinetics of chemical reactions as source terms in the Navier-Stokes equations. Even a coupling with a turbulent flow model is possible. However, describing the chemical kinetics of polymerization reactions under turbulent conditions still remains a challenge for which practical solutions are necessary. Such a simplification can be represented by hybrid modeling where different chemical and physical phenomena are separately simulated and coupled in an iterative manner. Consideration of the time scales of the ongoing phenomena is a critical step to decide for the appropriate coupling method and focus on the step with the highest process resistance.
The challenge during this project was to quantify the effect of the mixing behavior on the evolution of the polymer chain distribution of a living polymerization process. This chain length distribution is not only decisive for the application properties of the polymer product, but also for the fluid dynamics behavior during production. In addition, mass transfer and mixing of the dosed monomer in the reaction mixture play critical roles too. The coupling of fluid dynamics simulation in a stirred reactor with the modeling of the polymer chain distribution is realized by modeling a segregated reactor through calculating the material exchange rates. Critical parameters such as viscosity of the reaction mixture are taken form the kinetic simulation model for polymerization and considered in the CFD model. On the other hand, the material exchange rates for the segregated reactor model are obtained from the CFD simulations. These highly exothermic reactions required additionally the consideration of heat transfer, which was also implemented in the model to obtain temperature distributions in the reactor as illustrated. Laboratory scale experiments were supported with the help of the described modeling approach and the agitator design was optimized. Subsequently, the process was transferred to the pilot scale and then to production scale, for which the number of experiments was reduced and the time-to-market considerably shortened.
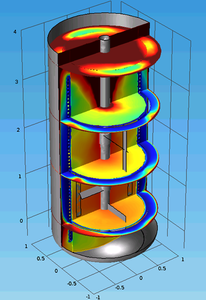
Téléchargement
- akgaan_poster.pdf - 1.44MB
- akgaan_abstract.pdf - 0.08MB