Numerical simulation of Proton Exchange Membrane Fuel Cells using COMSOL Multiphysics and elucidating the effect of different flow rates and temperatures
Dr. Mishma S Stanislaus1, Dr Lathapriya1, Dr Anand M Shivapuji2, Prof S Dasappa3
1 Research Scientist; 2 Senior Research Scientist; 3 Professor and Chair Interdisciplinary Center for Energy Research Indian Institute of Science; Bangalore – 560012
Proton Exchange Membrane Fuel Cells (PEMFCs) have garnered significant attention primarily due to their high efficiency. Modeling PEMFCs plays a pivotal role in optimizing their design, operation, performance and understanding their complex behavior. In this study, we employ COMSOL Multiphysics to develop a comprehensive numerical PEMFC model. The primary focus is on investigating the effects of different anode and cathode fuel flow rates across a specific temperature range on the PEMFC's performance characteristics. The developed PEMFC model considers a three-dimensional domain, accounting for the anode flow channel, anode, the proton exchange membrane, cathode and cathode flow channel. Further, simulated PEMFC model integrates Multiphysics phenomena, including mass transport, momentum transport, electrochemical reactions, and fluid dynamics, to capture the complex interactions within the PEM fuel cell structure. The electrochemical reactions are represented using appropriate kinetics (Butler-Volmer) and thermodynamics, while transport phenomena are described using Maxwell-Stefan diffusion and convection equations. Likewise, the flow distribution of the PEMFC model is addressed using Navier-Stokes and Brinkmann equations. The model's accuracy is validated against experimental data. To explore the effects of fuel flow rates, a parametric study is conducted, encompassing a wide spectrum of operating temperatures (30- 90 oC). The fuel flow rates are systematically adjusted (H2:O2 100:100, 100:200, 200:100 and 200:200) while monitoring key performance metrics such as cell voltage, current density, power density and overall efficiency. From the polarization and power curves, it is observed that as the temperature increases, the current density and power density values are decreasing gradually at all the fuel flow rates employed. The maximum current density and power values obtained at an optimized fuel flow rates of H2:O2 (200:100) are 61049 A/m2 and 13966 W/m2 at 30 o C. The difference in the current and power density values observed while varying fuel flow rates is due to fuel starvation or flooding which limits reactants transportation. The decrease in the current and power density with increasing temperature is due to the low concentration of H2O (0.001 mol%) employed in the model. Due to dry conditions inside the cell, the proton conduction inside the model is hindered, which in turn limits the current density. The distribution of reactants within the cell in accordance with varying fuel flow rates that affects the electrochemical reactions is also analyzed, in order to understand the performance of PEMFC. This study provides valuable guidance for optimizing PEMFC operation under varying temperature and fuel flow rate conditions. The developed COMSOL model serves as a versatile platform for further investigations into novel designs and advanced operating strategies.
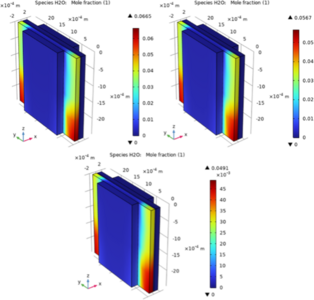
Téléchargement
- Mishma_7781_Poster.pdf - 0.91MB
- Mishma_7781_Paper.pdf - 2.15MB