Multi-Frequency Design of an Optimized Microwave Cavity for Plastic Recycling Applications
Microwave heating has been used in industry because of its pollution free and rapid heating technique [1]. It consists of an electromagnetic wave that passes through a media with a frequency between 300 MHz and 300 GHz [2] to generate heat in the system.
The purpose of the current work is to design and optimize the physical process of material heating inside a reactor using 9 ports emitting electromagnetic waves. Although several works are available in the literature concerning single-frequency simulation (S-F) for different geometries and applications [3-6], few papers are available using a multi-frequency (M-F) simulation. Therefore, this paper focuses on the 3D simulation of a reactor cavity using two levels of frequency (915 MHz and 2.45 GHz) with a power level of 51 kW. These two levels of frequency have been used because its convenience for industry applications.
Three different COMSOL Multiphysics® interfaces are used in this work. In these modules, Maxwell equations, Poynting theorem, and energy conservation law are used to simulate the electromagnetic heating [7]:
- Electromagnetic Waves, Frequency Domain, defining, model boundaries and number of ports, power and its work frequency.
- Heat Transfer in Solids/Fluids, required to evaluate heat transmission inside the study domain.
- Electromagnetic Heating Multiphysics coupling, converting electromagnetic waves distribution inside cavity into energy penetrating inside study domain as heating.
The main expected results consist on:
- Homogenization of the EM field distribution after the sensitivity study analysis varying both the frequency, number of ports and position.
- Decrease of heating time required to reach objective temperature of the application: (180-200 ºC)
- Optimization of temperature distribution inside reactor, especially focused on hotspots.
Acknowledgments
The project has received funding from European Union’s Horizon 2020 research and innovation programme under the grant agreement No 820665-polynSPIRE project. This publication reflects some preliminary results from a MW simulation required inside the H2020 polynSPIRE project, focused on technologies of plastic recycling.
References
[1] M. R. Hossan, D. Byun, and P. Dutta, “Analysis of microwave heating for cylindrical shaped objects,” Int. J. Heat Mass Transf., vol. 53, no. 23–24, pp. 5129–5138, 2010.
[2] G. Roussy and J. A. Pearce, “Foundations And Industrial Applications Of Microwaves And Radio Frequency Fields. Physical And Chemical Processes.,” in Wiley, 1998, pp. 115–116.
[3] E. Ethridge and W. Kaukler, “Finite Element Analysis of Three Methods for Microwave Heating of Planetary Surfaces,” 2014.
[4] D. S. Rajpurohit and R. Chhibber, “Design Optimization of Two Input Multimode Applicator for Efficient Microwave Heating,” Int. J. Adv. Microw. Technol., vol. 1, no. 3, pp. 68–73, 2016.
[5] H. Nigar et al., “Numerical analysis of microwave heating cavity: Combining electromagnetic energy, heat transfer and fluid dynamics for a NaY zeolite fixed-bed,” Appl. Therm. Eng., vol. 155, no. July 2018, pp. 226–238, 2019.
[6] T. Santos, L. Costa, and M. Valente, “3D electromagnetic field simulation in microwave ovens: a tool to control thermal runaway,” COMSOL Conf., pp. 3–7, 2010.
[7] L. A. Campañone and N. E. Zaritzky, “Mathematical analysis of microwave heating process,” J. Food Eng., vol. 69, no. 3, pp. 359–368, 2005.
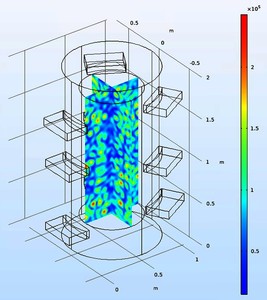