- Bridging the Terahertz Gap
- Modeling the Lithium-Ion Battery
- Protection contre la Corrosion
- Modélisation des batteries
- Modélisation et Simulation dans le développement des piles à combustible
- Modélisation thermique des petits satellites
- Analyse électro-vibroacoustique d'un transducteur à armature équilibrée
Implementation of specific surface condition to describe induction heating of multilayered materials
Induction heating is used in lot of applications: forging, brazing, hardening, melting, bonding. The main advantage is ability to heat quickly, efficiently, and locally with a good repeatability. It leads to productivity and energy efficiency improvement. These solutions are often used in packaging and electronics applications (Printed Circuit Board) for bonding or sealing efficiently plastic materials: for example, a multilayered material constituted by a stack of conductive layers (copper) and non-conductive layers (prepreg resin or thermoplastic polymer). A transverse electromagnetic configuration is needed for a good heating efficiency of the conductive layer. It can be achieved with pin-shape inductors on both sides of the stack with a frequency range around 300 to 1000 kHz to generate mainly a transverse magnetic field through the stack. An interesting modelling approach for these induction heating processes is to replace the thin metallic sheet by a surface description (Transition Boundary Condition). In case of a multilayered materials meshing difficulties can occur due to dimensions ratio between thickness and length of the isolating layer. An extension of these approaches to multilayered materials for AC field was implemented to avoid these problems: the whole multilayered material is replaced by one surface condition. A simplified 2D approach is used to validate this specific surface condition (named ‘double TBC’) and compared with analytical description based on wave propagation. The ‘double TBC’ surface condition simulates a multilayer material constituted by two copper layers (10 µm) and one insulating layer inserted between metallic layers (100 µm). A 3D COMSOL Multiphysics® model is set up to describe the heating of these multilayered materials thanks to a pin shape inductor by considering such ‘double TBC’ approach. The model consists of a coupling between electromagnetics (vector potential A and frequency domain formulation) and heat transfer in shells with multilayered materials interface.
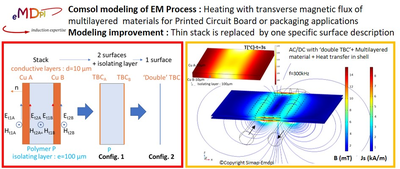