Fluid-Structure Interaction of Coupled Valves in Sucker Rod Pump
Motivation
We simulate the fluid driven interaction between two dynamically coupled valves designed to work in conjunction with each other. Such interacting valves are extensively used in sucker rod pumps for oil extraction. These pumps essentially consist of a pair of ball check valves inside along tubing that reaches down to the oil reservoir. One of the valves is fixed at the bottom of the tubing and is called the standing valve (SV), whereas the other oscillates up and down the tubing above the SV and is called the traveling valve (TV). During the upstroke, the TV is closed and acts as a syringe sucking the fluid through the, now open, SV into an expanding chamber between the two valves. On the downstroke, the fluid collected in the chamber is forced up into the tubing as the check ball of the SV closes the valve and the TV is open. The opening and closing of the valves are governed by the flow of the fluid being pumped, and hence we are solving a fluid-structure interaction problem.
Method
We are able to simulate the entire pump cycle described above in COMSOL Multiphysics®, including the closing/opening of the valves implicitly.
- This pump model is set up by employing the Moving Mesh (ale) interface, and the fluid flow is simulated using the Laminar Flow (spf) interface.
- The stress was integrated over the ball surface to compute the drag force on the balls, which was used in Global Equations node to solve a set of coupled ODEs for the position of the balls of the two valves as a function of time (similar to COMSOL Multiphysics® Application ID: 12655). The solution was used to impose the displacement of the moving mesh of the balls and the TV.
- Simulating valve closure is a particularly challenging task since the fluid continuum breaks down during closing. This was overcome by applying a repulsive force on the balls when they came closer than a critical distance to the valve seat. The ball could come as close as 1/500th the radius of the ball to the valve seat, practically closing the valve.
- The center of the gap between the ball and the seat was computed as a function of time using the General Extrusion Component Coupling, and was used to probe the gap pressure at this position.
Conclusions and Broad Implications
As far as we know, this is the first time both standing and traveling valve dynamics are combined in a single FE model. We have used real data from oil fields as input to our model and have identified a new scenario that we call mid-cycle valve closure, which could be potentially dangerous to the pumps. Using our model we can also predict the likelihood of the scenario occurring in real pumps, and hence take measures to avoid it. Parametric study of pump design parameters can be performed to optimize the valve geometry for improved pump operation.
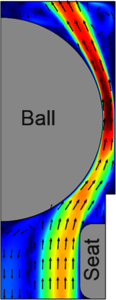