- Bridging the Terahertz Gap
- Modeling the Lithium-Ion Battery
- Protection contre la Corrosion
- Modélisation des batteries
- Modélisation et Simulation dans le développement des piles à combustible
- Modélisation thermique des petits satellites
- Analyse électro-vibroacoustique d'un transducteur à armature équilibrée
CFD-based Approach For Prediction of Headspace Pressure In Can During Thermal Sterilization of Foods
Thermal sterilization is a critical process in the food industry as it ensures the safety and shelf-life of food products for long-term preservation by eliminating all microorganisms and their spores from a food product. This process requires huge energy and water consumption, and results in nutritional destruction (Dutta et. al, 2024). For these problems, the food industry requires new non-conventional sterilization processes with less energy demand and water consumption and higher retention of nutrients. But, prior to the development of new effective non-conventional processes, it is necessary to monitor the process and also to predict internal pressure of containers with foods during the sterilization process. This is one of the key factors that helps to design new packaging for both conventional and non-conventional sterilization processes. As per our knowledge, there are very few studies that investigated this problem. Hence, the objective of this study is to monitor and predict these internal pressure using Computational Fluid Dynamics (CFD).
The aim of the present work focuses on the study of pressure evolution in the headspace and temperature evolution at different locations in a model food during a conventional retort sterilization process. A simple 2D CFD approach without mass transfer was used to assess the pressure increase within the headspace. For this purpose, numerical simulations using COMSOL® Multiphysics 6.2 were conducted and vapor pressure was calculated by analyzing experimental and simulated pressure results.
Numerical simulations were conducted to analyze the heat transfer and fluid flow phenomena inside the can during thermal sterilization process (Heat Transfer and CFD modules were used). The Navier-Stokes equations were incorporated for the study of velocity and pressure fields of fluid within the headspace of the can, which is crucial for understanding the heat distribution through convection and the pressure evolution.
A 2D-axisymetric model of the metal can with mashed potato (model food) was generated using the geometry node in COMSOL® (Figure 1). Thermophysical properties linked with temperatures were incorporated as input parameters. Material properties such as dry air was imported from the application library and mashed potato material properties were imported from experimental measurements. A physics-controlled mesh with fine element size was used for the numerical modelling. The study was computed from 0 s to 8340 s with mesh size of 1681 elements.
Simulations showed evolution of temperature and dry air pressure in the headspace of the can (Figure 2). The maximum pressure generated by dry air was 1.4 bar (absolute) at 4821 s. The experimental pressure values were imported into COMSOL® as an interpolation function. The experimental maximum total pressure in the headspace was 3.45 bar (absolute). Evaporation rate inside the can was calculated and this was coherent with experimental measurements.
This study lays the groundwork to explore pressure evolution in alternative non-conventional sterilization processes such as microwave sterilization, where heat transfer is through volumetric heating, unlike the conventional thermal sterilization process. The insights gained from this present study of COMSOL® modeling can be applied to develop effective packaging for both conventional and non-conventional processes.
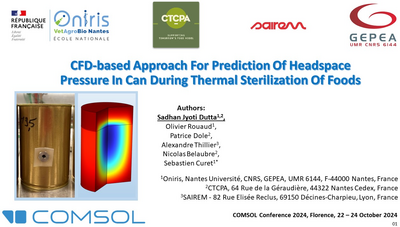
Téléchargement
- dutta_9651_poster.pdf - 0.99MB
- cfd-based-approach-for-prediction-of-headspace-_sadhan_comsol.pdf - 0.94MB
- 4_sadhan_jyoti_dutta.pdf - 1.94MB