Accelerated Electrochemical Machining Tool Design
Electrochemical machining (ECM) is a manufacturing technology that allows metal to be precisely removed by electrochemical oxidation and dissolution into an electrolyte solution. ECM is suited for machining parts fabricated from “difficult to cut” materials and/or parts with complicated and intricate geometries. In ECM, the workpiece is the anode and the tool is the cathode in an electrochemical cell; by relative movement of the shaped tool into the workpiece, the mirror image of the tool is “copied” or machined into the workpiece. One notable difficulty with ECM is the challenge of predicting a priori the tool and process parameters required in order to satisfy the final dimensional specifications of the fabricated part. This talk will present preliminary results demonstrating the potential for COMSOL Multiphysics® simulations to enable a phenomena-based design platform for prediction of optimal ECM tool shapes. This capability is anticipated to dramatically shorten ECM process/tooling development cycles, eliminating much or all of the iterative prototyping necessary at present.
This work represents a preliminary validation of the predictive tool design concept, comparing COMSOL® simulation predictions of machined profiles with optical profilometry data from corresponding direct-current ECM experiments. The ability of Primary Current Distribution and Deforming Geometry physics to predict the machined forms across a small test matrix of experimental parameters [electrolyte salt (“active” sodium chloride vs “passive” sodium nitrate) and electrolyte flow/tool geometry (“cross-flow” past a solid tool, and “flow-through” in a tubular tool)] was examined. While the simulation geometries were adapted to the different tool geometries, no account was made of flow effects, surface polarization, mass transfer limitations, or the different chemical properties of the two electrolyte salts. Thus, quality predictions were obtained for only a subset of the experimental conditions examined. For example, the COMSOL® predictions of the profiles machined with the rod tool were excellent for the nitrate electrolyte, but rather poor for the chloride electrolyte (Figure 1), though the fit was confounded by non-ideal (non-axisymmetric) machining of the test parts, presumably due to flow effects in the inter-electrode gap. The large scale of the geometric deformations occurring in these simulations posed significant challenges to the ability of the COMSOL® software solvers to remain well conditioned, with numerous errors arising from inverted mesh elements and deviations of nominally fixed mesh boundaries from their initial positions. Further development in terms of both the fundamental design of the simulations and the physics incorporated therein will be required.
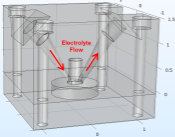
Téléchargement
- skinn_presentation.pdf - 1.56MB
- skinn_abstract.pdf - 0.25MB